I wrote the following article on Berthold’s matrices with Kerstin Wallbach from the Stiftung Deutsches Technikmuseum Berlin. Our original German-language text was published by the Staatsbibliothek zu Berlin on its blog last week. Since 2020, I’ve been a member of the scientific advisory board a digiS digitization project called Die Sichtbarmachung des Sichtbaren – Berlins typografisches Kulturerbe im Open Access. The Deutsches Technikmuseum coordinates this project, together with the Staatsbibliothek zu Berlin, the Erik Spiekermann Foundation gGmbH and the Kunstbibliothek of the Staatliche Museen zu Berlin.
What is typecasting?
Typecasting refers to the production of movable metal letters from a metal alloy comprised of lead, antimony and tin, etc. The casting process itself can be complex. Thanks to changes in printing over the last century and a half, the demand for fresh fonts of metal type is relatively low today. Unfortunately, this makes typecasting is an activity with an uncertain future. Rainer Gerstenberg, who operates the last commercial typefoundry in Europe, will retire at the end of this year. We’d like to draw your attention to a recently published interview with him (video, 69 minutes) as well as this 2019 article by Ferdinand Ulrich for Eye magazine.
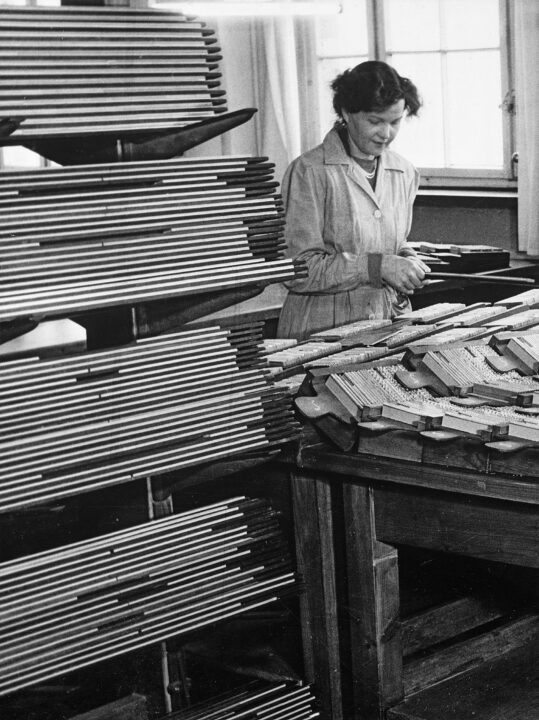
An employee at H. Berthold AG fonting type. Rows of freshly cast sorts from the typecasters are on wooden type sticks to her right (left-hand side of the photograph). Berlin, circa 1950. SDTB/photo: Hist. Archive.
Since typecasting has an uncertain future, as much information about it should be secured for the future as possible. The materials can then be provided to the various interest groups regularly dealing with type and media. For instance, some people learn about it during professional training courses or academic studies. Yet, the material is valuable for professionals from fields working to preserve written cultural assets, and the material could also be relevant in trademark law, etc. H. Berthold AG’s matrix collection was donated to the Deutsches Technikmuseum in 1993. When it comes to preserving typecasting materials and information about their use, this collection forms an important asset. Its presence within a museum can provide additional reference points for the already-mentioned digitization project. Die Sichtbarmachung des Sichtbaren – Berlins typografische Kulturerbe im Open Access will digitize three public collections’ type specimens from Berlin-based typefoundries and typesetting-machine manufacturing companies and make them accessible online. Or, at least, those specimen printed up to 1951.
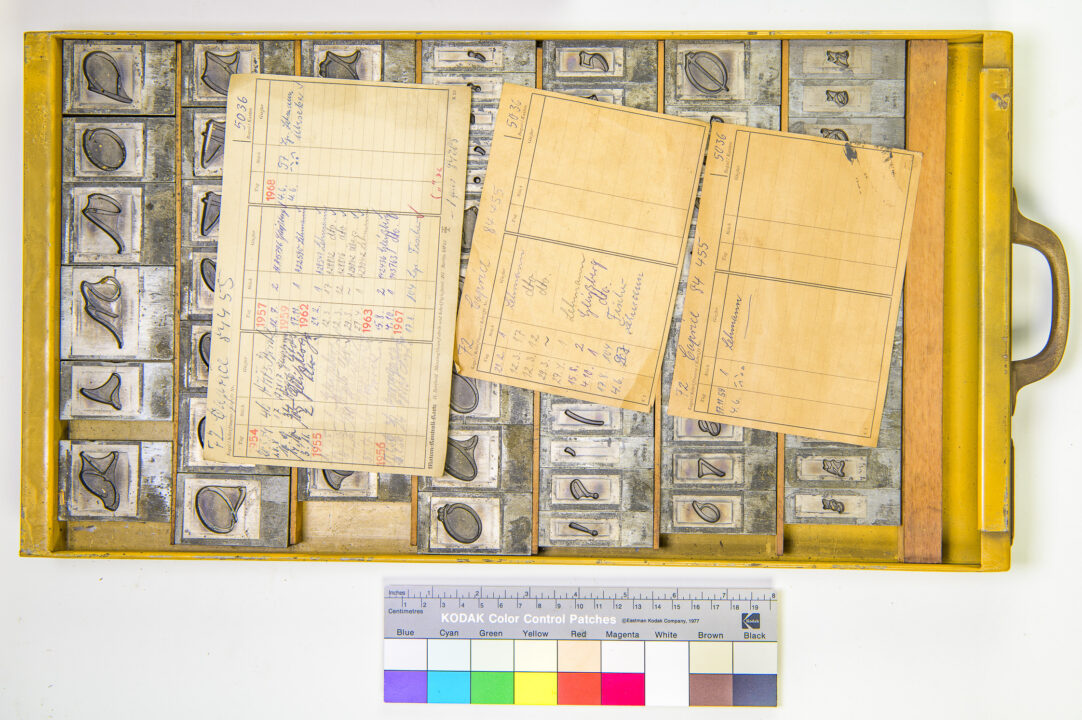
Drawer 21 with 65 matrices and three casting slips for the »Caprice« typeface’s 72pt size. SDTB/photo: Malte Scherf. Click to enlarge.
The Deutsches Technikmuseum and H. Berthold AG
The Deutsches Technikmuseum’s first documented contact with H. Berthold AG dates back to a time before the museum’s founding. Günter Gottmann was the first director of the Museum für Verkehr und Technik, as the Deutsches Technikmuseum was originally known. On 18 February 1982, he sent a letter to a member of Berthold’s board, recounting a company “treasure cellar” that a museum employee had recently visited. Berthold had rescued the items in this cellar during what had been described as “difficult years” for the company, particularly through the efforts of an employee named Mr. Bleicke. Berthold was still doing business in 1982; Gottman was writing in the context of the company’s upcoming 125th anniversary, planned for 1 July 1983. His letter justifies the museum’s interest in Berthold’s holdings. On the one hand, he described its “necessity of maintaining and documenting the history of Berlin’s important businesses.” On the other hand, the museum should present moveable type as “an important step in how writing had been presented historically, as part of developments leading to the photo-typesetting technology unfolding in the present day.” (We should note that the first computers were already around at this time.) For the planned museum’s permanent exhibition on writing and printing technology, also scheduled to open in 1983, he received various objects of “technical equipment and products of the Hermann Berthold type foundry and brass-rule factory, founded 1 July 1858.” These are still part of the museum’s revised permanent exhibition today, even though it is not possible – as had initially been planned – for their functionality to be demonstrated to visitors. Since the 1980s, the Deutsches Technikmuseum has continuously expanded its holdings from H. Berthold AG. This article focuses on the matrix collection in the museum’s external depot and the associated reference castings and casting slips. H. Berthold AG items also represent part of the museum’s Historical Archive and Library, as well as in the museum’s collections of physical artifacts.
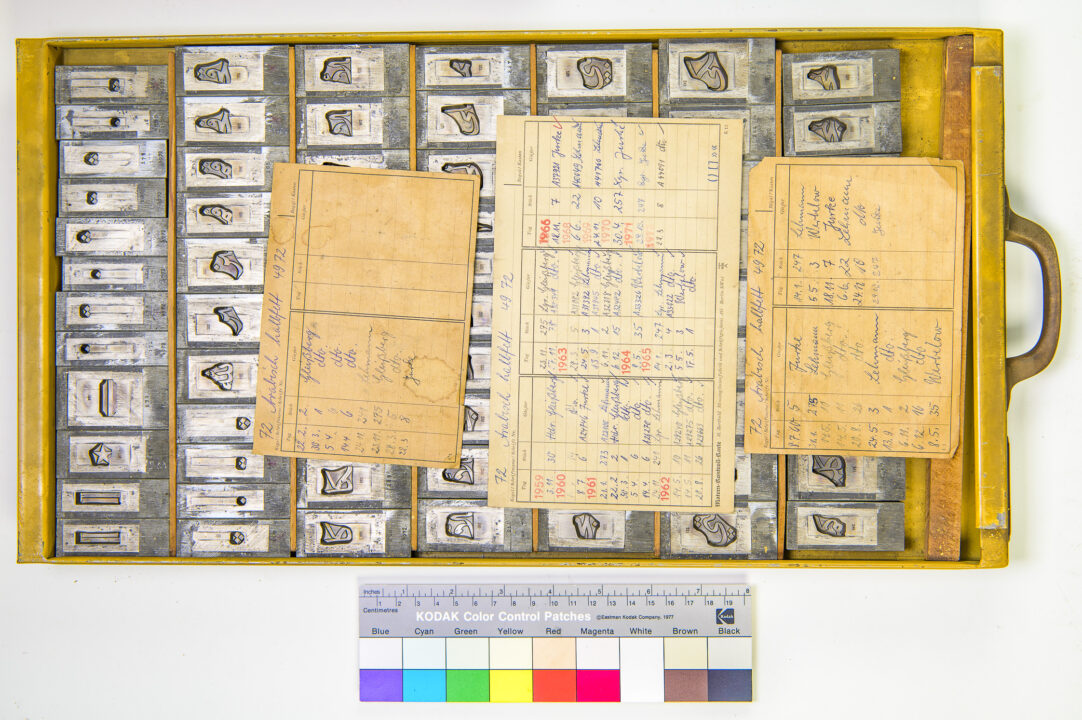
Drawer 17 with 70 matrices and three casting slips for a 72pt-size Arabisch halbfett typeface [Arabic Bold]. SDTB/photo: Malte Scherf. Click to enlarge.
Matrices as museum artifacts
Even into the middle of the twentieth century, most printed texts (including type specimens) were composed with metal letters. Sets of molds called matrices were necessary to cast a font of movable metal type’s sorts. Matrices were something like the “heart” of the movable metal type ecosystem. Historically speaking, the rights to cast a font of type were directly linked to the material ownership of these matrices. Punches and matrices helped e typefounding possible. In some instances, they may have even essentially provided a “license to print.” The Deutsches Technikmuseum’s collections also include the surviving punches from the internal typefoundry inside the Berlin-based Reichsdruckerei and Decker printing house.
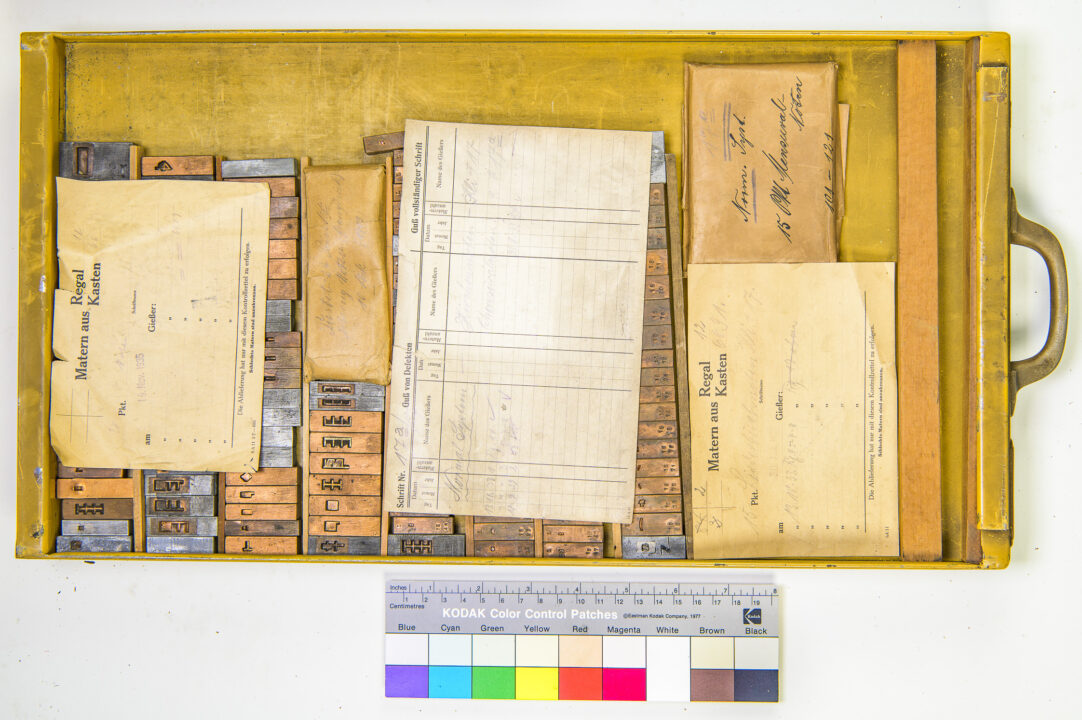
Drawer 34 with 186 matrices and three casting slips for musical notation fonts in 15 pt. SDTB/photo: Malte Scherf. Click to enlarge.
As it does today, typeface manufacturing in Berthold’s time straddled fault lines running between various areas, including new product development, intellectual property, licensing agreements and distribution networks based on particular economic interests. Like other large type foundries, Berthold had advertising, patent and legal departments. For various reasons, it often dealt with major technological upheavals retrospectively, without much foresight. Several printing technologies were used in parallel for long periods. That was necessary, among other reasons, because of legally-binding maintenance and service agreements Berthold had with existing customers. It was also caused by Berthold’s customers often having specialized focuses. They had already made significant investments in Berthold’s products. To this, you can add regional peculiarities and the scarcities of resources and historical transformation processes brought about by two World Wars. Since Berthold was based in Berlin, it was also directly affected by the post-war division of Germany. The fates and interests of many Berthold employees were dramatically affected by the factors mentioned above. In some cases, they had to reorient themselves professionally multiple times, a fact reflected in their individual employment histories.
It was the typecasters who spaced designers’ typefaces
How did the practical cooperation between type designers – who into the 1960s were still referred to in Germany as Schriftkünstler – and persons in a typefoundry’s management who were responsible for them unfold? What relationships did type designers have with the employees working in a foundry’s various departments, like manufacturing, sales and advertising? These are relevant questions for typefaces and type sizes that were actually cast – instead of simply being selected from an on-screen menu.
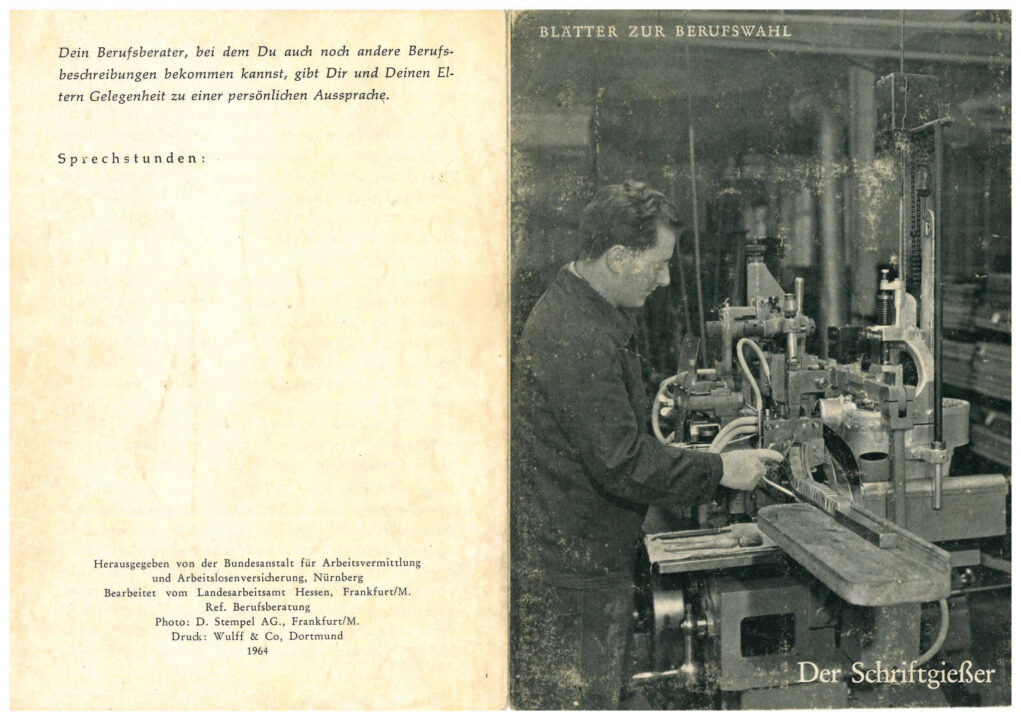
»Der Schriftgießer«, Blätter zur Berufswahl, 1964. Image: Staatsbibliothek zu Berlin – Preußischer Kulturbesitz.
From interviews with Manfred Weber, We know that about 100 people at Berthold were involved with the production of metal type fonts in the 1960s. These employees were divided up across areas like punchcutting, electroplating, justification, typecasting and fonting/packaging. The figure also included brass-rule manufacturers and machinists. Weber started an apprenticeship as a typecaster at H. Berthold AG on 1 April 1960. He worked at the company until 30 September 1967. In 2018, Manfred Weber recalled how the collaboration between a type designer and Berthold’s typecasters worked, saying that:
Before the typecaster’s work began, various upstream processes regarding type design and cutting had to happen. The type designers worked closely with the punchcutters; they basically worked hand-in-hand. Whatever the type designers specified in their drafts was later implemented by the punchcutters. The electroplating department could then make a typeface’s first matrices. These were the molds needed to cast a font. After its matrices were made, a typeface was sent to the typecasters, who cast trials with their machines. The typecaster determined how much space would come between the letters, as well as the spacing for each letter individually. The type designer would then decide whether this was good or not. The one-or-the-other letter would then have to be made a bit tighter or looser or have its horizontal position changed otherwise. After his typeface was printed, the type designer approved it. He was something like the lord of the typefaces: he was the one who decided if it was that good or not. Later, the typeface went into production. While putting a typeface’s spacing together, the typecaster always made the best go of it; at some point, the type designer would say, “yes, that’s good, that’s the width it should have.” Once the width of an individual letter was determined, it was set for eternity.
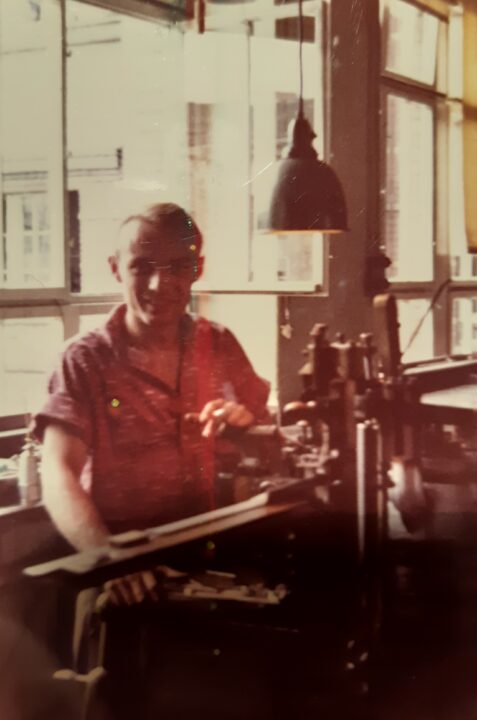
Manfred Weber, typecaster at H. Berthold AG, early 1960. Image: Private collection.
Most typecasters spent their entire lives within a single company. When asked in 2017 if he felt a bit cheated after aligning his life toward a profession that disappeared such a short time after he began working in it, Weber replied, “no, you can’t say that. One was attached to it, to one’s job, it was a good time. But you can’t say that one felt cheated. Look, would I be standing here otherwise?” That latter sentence refers to his willingness to show us a visible path into the future through interviews, his training materials, tools and photos – a significant contribution to our understanding of the development of typefaces as the basis of our knowledge and our current codes. This conversation and digitized copies of the textbooks he used during his 1960–1963 apprenticeship will form part of a series of interviews about H. Berthold AG to be published soon. Other interview partners include Alexander Nagel, Erik Spiekermann and Armin Wernitz. Together, these four interviews will provide prominent insights into the digital transition era as it has unfolded in Berlin since the 1960s.
H. Berthold AG’s matrices
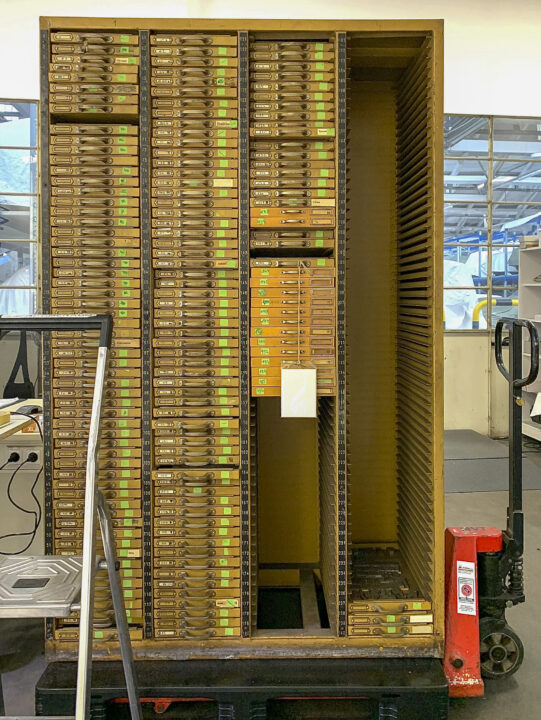
Cabinet with matrices from H. Berthold AG, drawers 001–240. SDTB/photo: Malte Scherf.
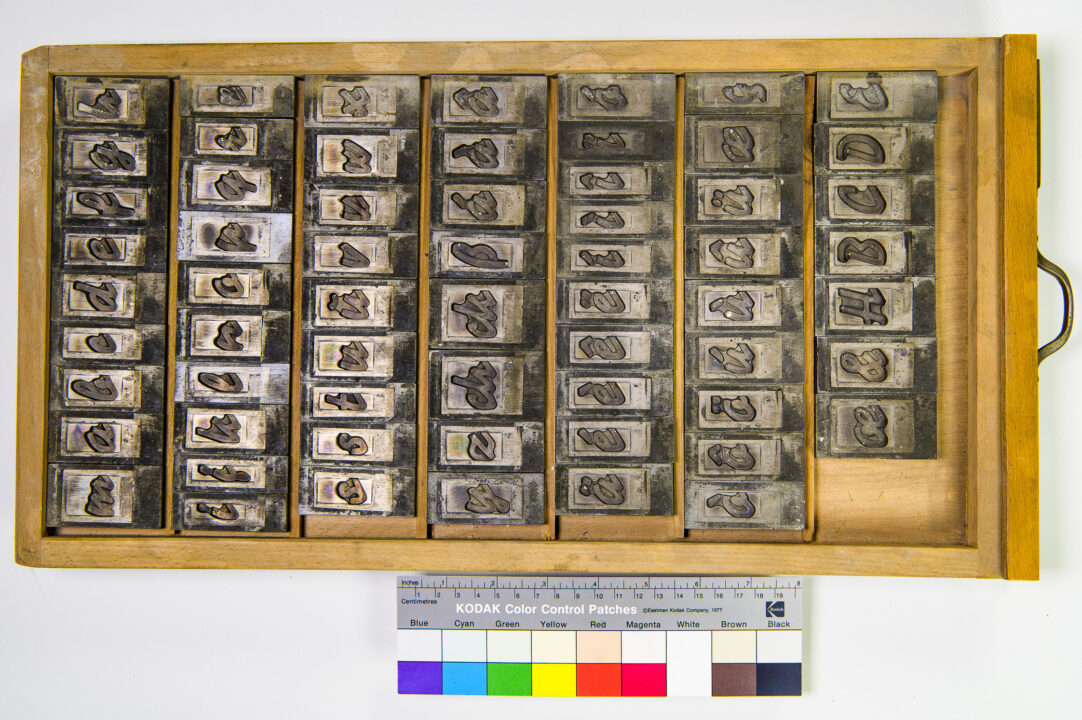
Drawer 144 with matrices from the »Signal« typeface’s 84pt size. SDTB/photo: Malte Scherf. Click to enlarge.
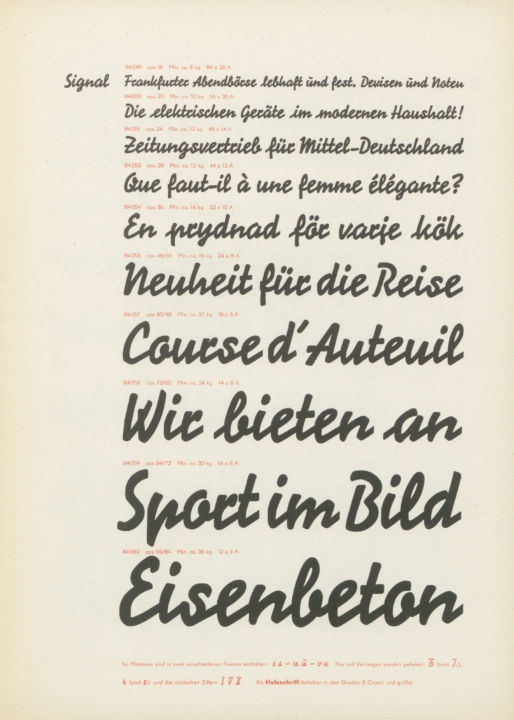
Page from an H. Berthold AG type specimen brochure for the »Signal« typeface. STDB/Hist. Archiv III.2-24399. Matrices for the 84pt size of this typeface are shown in the photograph directly preceding this one.
Near the end of the Second World War, several bombs hit the Berthold factory. Its stores of type were destroyed in the fire. Related to this, we recently found a postcard that Berthold sent as a reply to a customer inquiry in 1946. Its message relayed that the company’s type specimens – or at least the copies available for distribution? – had been destroyed by the events of the war. Among the H. Berthold AG matrices still kept in Berlin, however, there still may be a few that predate World War II (see, for instance, the 84pt matrices of Berthold-Fraktur reproduced below). The contents of these drawers are sorted by point size. They are currently being photographed in high resolution by photographers from the Deutsches Technikmuseum and compared with the museum’s (digitized) inventory lists from 1993 and other documents. In these lists from 1993, the drawers 001 through 470 are itemized in direct relation to Berthold’s indexing system, for which there is an additional card catalog including matrix control cards, for instance. The matrix drawers numbered 157–240 are not mentioned in the lists. They could be the portion of Berthold’s matrix inventory that we presume to have been sent to the Letternservice Ingolstadt in 1978. Based on a licensing system, this typefoundry continued the casting and selling Berthold types from that point onwards. The sale of Berthold fonts through the Letternservice Ingolstadt enabled Berthold’s customers to be resupplied, even though Berthold had fully transitioned to phototype and was no longer casting metal type itself. Access to research data and image material through digitized projects should make joint and cross-institutional research easier to perform in the future.
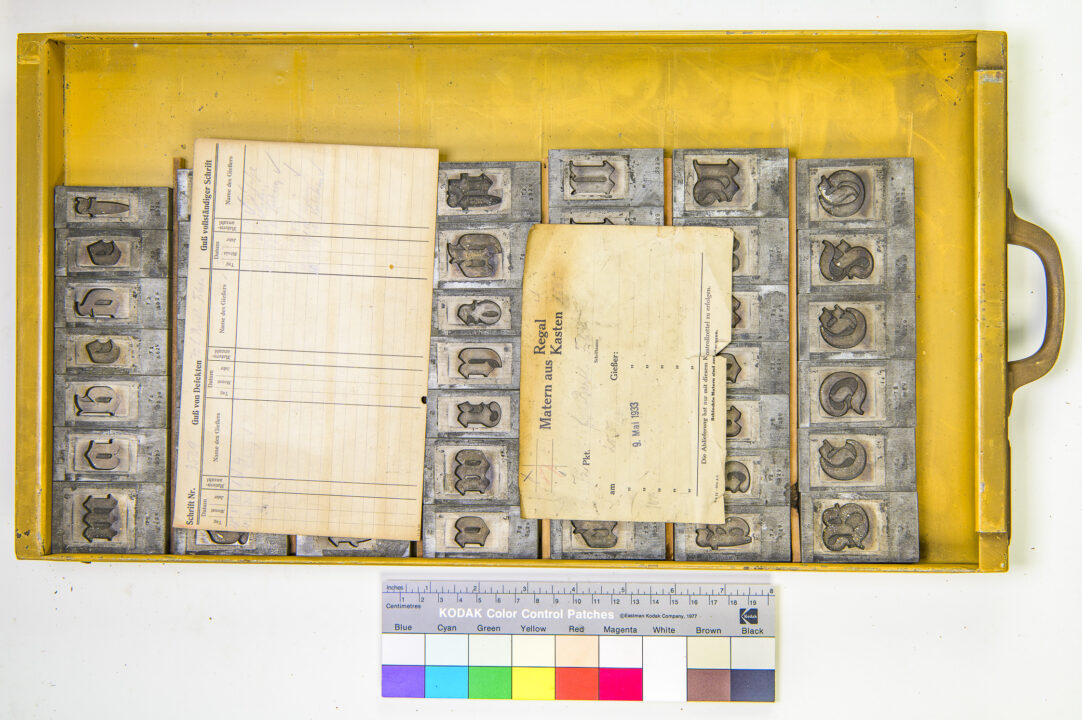
Drawer 32 with 50 matrices and two casting slips for the »Berthold-Fraktur« typeface’s 72pt size. Note the »9. Mai 1933« stamp on one of the slips; these matrices certainly predate the Second World War and the subsequent damaging of Berthold’s main factory in Berlin. SDTB/photo: Malte Scherf. Click to enlarge.
The casting slips in the matrix drawers play a crucial role in this. Regarding the Berlin stock, we estimate that about 800 casting slips are in the matrix drawers. These represent an important primary source for researchers. They provide specific data on the company’s workflow, including the names of the typecasters, the number and condition of the characters, how often and when different typefaces have been cast, how successful a typeface was – or whether it was able to be successful on the market, etc. The poor quality of cellulose paper in technical documents is a widespread reality in technical museums. When it comes to the casting slips, however, there is also corrosion-related degradation processes and heavy pollution from their usage and storage contexts to consider. Here, too, it will be exciting to see which paths different institutions and actors will take in the future because of the significant challenges. Ideally, this path will be followed together – as we have often seen when it comes to “Berthold.” Our clear goal is to enable people to access the products of a very special Berlin company with them, wherever they are.